Screen printing is widely used due to the low cost and vast choice of colors. It’s a common private labeling method. But very few explain “what screen printing is” in a practical way. So, I write today’s article, with a focus on the following 4 aspects.
- What is Screen Printing?
- How Much Does Screen Printing Cost?
- Screen Printing Pros and Cons
- Screen Printing Basics & Materials: Screen, Squeegee, 3 Common Inks
Believe that you’ll have a better understanding of screen printing techniques after reading. You can navigate to related content via the above links.
What is Screen Printing?
Screen printing definition given by Wikipedia is a printing technique where a mesh is used to transfer ink onto a substrate, except in areas made impermeable to the ink by a blocking stencil.
In simple terms, screen printing is a printing technique transferring images onto the product surface with the help of a screen, ink, and squeegee. It’s also knowns as silkscreen printing as the early screen is woven by silk.
In our daily life, we often see T-shirts with screen-printed images, as shown in the picture below. It can improve the fabric look and realize private labeling.
How Much Does Screen Printing Cost?
Screen printing cost = plate-making charge + printing labor charge/pcs.
- Platemaking usually charges from $15 to $70. The plate is applied one color at a time. The more colors you print, the more plates manufacturers need to make. Correspondingly, you pay more.
- The printing labor fee is around $0.03/pcs. The MOQ for screen printing is at least 500 pcs/item.
Case Sharing
One of our clients purchased 1000 pcs of the coffee silicone, foldable cup with a custom logo as shown in the image right. The logo was screen printed and the total printing charge was $60.
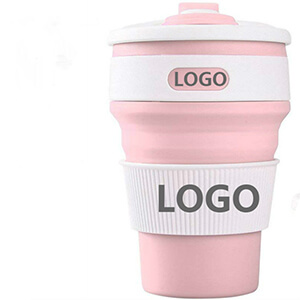
A Useful Takeaway
The screen-printing cost is determined by how big the pattern is, how many colors are needed, and how many to print. The more you order, the lower price you get. Once you buy more than $2,000/item, most Chinese factories can offer you a free screen-printing service.
Screen Printing Pros and Cons
Screen printing techniques can be applied to a great many objects, except water and air. There is such an interesting comment: if you want to find an ideal printing method on the earth and achieve the printing purpose, it is likely to be screen printing. Why? That should be attributed to some good features.
Advantages of Screen Printing
1. Wide Applicability and Great Flexibility
- Good for a simple design.
- Applied to almost all materials-made products such as business cards, plastic toys, etc.
- Printed on flat, curved, and spherical surfaces of either hard objects like glass or soft objects like fabrics.
- No limit on its target printing area, like 3 meters × 4 meters and even bigger.
- Manual & automated printing are used, one for the small print, the other for mass print.
2. Long Lasting and Durability
- Hard to fade alongside temperature or sunlight changes. This helps save costs for sticker production.
- More suitable for outdoor ads and signs.
3. Good Quality and Third-dimensional Sense
- The texturized effect rendered by silkscreen art is good, with a 3D look and feel.
- The color is vivid and bright, even on darker fabrics.
- One screen is used for a distinct color, so different screens can be used to realize multi-colored image printing.
4. Affordable Cost and Best for Large Orders
- Convenient plate making and lower price than other printing methods.
- Easier and more cost-effective for huge quantities (especially custom clothing), cuz a stencil can be used to repeat designs many times.
Drawbacks of Screen Printing
- Unsuited to low volume printing because of the high setup costs.
- Not suitable for multi-colored patterns that have high skill requirements, especially gradient color design.
- Less friendly to the environment due to the pollutants generated by the used ink plus plate making and cleaning process.
Screen Printing Basics and Materials Used
The fundamental principle is to print by pushing out the ink from a screen mesh. And the screen printing process is easy to operate through such 5 simple steps as follows.
- Create designs or patterns.
- Make the screen plate.
- Coat emulsion and expose it to light to obtain a stencil.
- Ink up and print the design on the product.
- Dry and clean the screen for reuse.
Tools and materials for screen printing mainly include the silkscreen and screen plate, squeegee, ink, press, and substrate. It’s easy to understand “the press”, which is used to improve the efficiency of screen printing. So as for the “substrate”, it refers to the materials a pattern is printed on. Fabric, paper, glass, or plastic are most seen.
The Silk Screen and Screen Printing Emulsion
The screen is the most fundamental and consists of a metal or wooden frame plus a fabric woven mesh. In most cases, the fabric directly leads to the printing quality.
So, what’s the best fabric for screen printing? In the very beginning, silk was used for the mesh fabric. Later polyamide (nylon), polyester, and stainless steel are widely applied. These synthetic fabrics perform well as silk yet at a lower price. High-quality fabrics have good features in common, and I summarize them as follows:
- High mesh count, in other words, tight weave.
- Hard to shrink or react with the print paste.
- Able to withstand any stress and hard to stretch out when in use.
- Anti-moisture and dyed with ease.
- Cost-effective.
The screen-printing emulsion is important for it’s coated on the screen to prevent the ink from passing through. After that, there comes a step of exposing it to light. Then, it’s ready to be used as a stencil. Once the printing finishing process ends, it needs to clean and then can be re-used.
The Squeegee
It’s a rubber blade with a handle, used to push the ink through the mesh screen and onto the surface beneath. Manual screen-printing favors squeegees made from natural or synthetic rubber such as polyurethane. While in the case of automatic screen printing, silicone rubber squeegees are more often used, with a similar size to the screen frame for better coverage.
To meet different screen-printing needs, there exist different squeegee firmness or durometer. Commonly seen are 75-85 durometer. A firmer squeegee is preferred to screenprint fine details involved in complex patterns. While for relatively simple designs or screen printing on fabrics, a softer squeegee is needed.
3 Common Types of Screen Printing Inks
The inks are more complex in comparison to the above silk screen printing materials. You might be confused about a great many types of inks and wonder which is right for your projects. The choice of inks drastically affects the printing effect. A good example is that we often see screen-printed bags, some of which look good, but some are terrible. That closely relates to the used ink. Here I list and explain 3 common types.
Plastisol Ink
The most common type. It’s always the first choice for the clothing industry for the good coverage, applications to most fabrics, plus little ink waste. But there’s a drawback — the thick feel. Using additives can be useful. However, it’s less environmentally friendly for some less sustainable ingredients.
Water-based Ink
This is an eco-friendly alternative to PVC-based plastisol inks. And it delivers prints into fabrics not remaining on the surface like plastisol ink. So, it’s more tailored to the increased demand for clothing soft hand. Plus, it’s more detailed than plastisol ink and longer-lasting than any other print. But there’re limits for fabrics as it only holds to cotton fibers. 100% cotton is needed for bright colors on dark garments.
Discharge Ink
It helps solve that issue by adding an activator to bring the garment back to its natural color and thus re-dyeing. It stands out for making the colors bright while keeping a soft hand feel.
Both water-based ink and discharge ink are great for retail brands for delivering super soft prints. But remember there exists a higher garment loss risk since the fabric is already dyed and prints are hard to fix. However, small imperfections can be fixed if printed with plastisol inks. So, you’d better order a couple of extras to make up for defective products.
Final Words
Actually, screen printing has a long history. It originated far back 2,000 years ago in China. Then re-defined by Japan and developed in Europe and America. This technique was confidential as industrial use for a long time. Up to the 1930s, it first appeared as an artistic medium, and the term “serigraphy” was created for artistic use. Till the 1960s, screen printing became popular under the influence of Andy Warhol and some other artists.
I believe this blog would give you a rough idea about screen printing. If still confused, you’re welcome to leave a message.
Our StrategicSourcing expertise starts with understanding your needs. As a leading sourcing company in China, we’ve helped many clients add private labeling for their products by means of screen printing, either on the product body or packaging. Feel free to CONTACT US.