Injection molding is a kind of production process which is widely used by almost all industries. And it is a common way to make customized products or do private labeling. Look at the table of contents below. And click the part you’re interested in.
Table of Contents
- What is injection moulding?
- How does it work?
- Injection molding cost (case sharing).
- Injection molding advantages and disadvantages.
- Four major factors for choosing the right injection molding services.
- Comparison of plastic, rubber, metal injection molding materials.
- Five common plastic injection moulding materials.
- Common injection moulding applications (household, food & beverage).
What is injection moulding?
Injection molding is a process to produce parts in large volumes by injecting molten materials into molds. Moreover, many products in daily life are made by the process like cups, toys, keys, and so on. Besides, many materials can be used, mainly including plastic, metal, glass, rubber, and so on.
How does injection molding work?
Once the mold is created, it‘s loaded into the injection machine. And then the process begins. Put material granules into a hopper; melt in the barrel; inject them into a mold. Then it cools and solidifies into the shape of a part. At last, the part is ejected out.
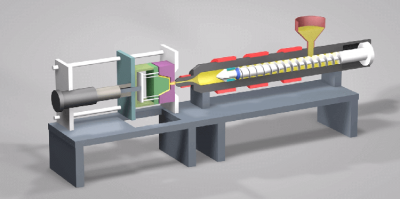
Image Source: 3ERP
Generally, the process includes six simple steps. They are camping, injection, dwelling, cooling, mold opening, removal of products.
Injection molding cost
Strictly speaking, injection molding cost = Equipment cost + Mold cost + Material cost + Labor cost. The mold cost and labor cost are higher.
Actually, the factory will charge you for replacing the mold or creating the mold for custom injection moulding. According to TWI, usually, the mold cost ranges from $1,000 to $5,000. Very large or complex molds are more expensive up to $80,000, or even more. The specific price depends on the products.
In my years of customized product experience:
- A mold for plastic items usually costs $1,000 to $3,000. MOQ is about 300 to 500 pieces.
- A mold for rubber parts will cost more, and higher MOQ, more than 3000 pieces, because it’s more complex than plastic injection molding during the process.
- While for metal products, the mold price is lower, $500 to $1,000.
Rubber injection molding case sharing:
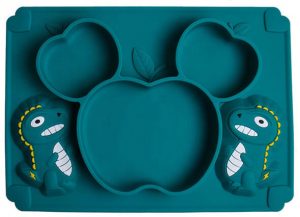
Help Me Injection molding & Customize
One of my clients purchase 3000 pcs of silicone baby plate as shown on the left.
The mold cost is $1900.The cost of labor and material is $6472. So the total cost is $8372.
Note: This picture is from Alibaba, not our customer’s product, just for reference.
Injection molding advantages & disadvantages
As mentioned before, injection molding cost is not low. So you have to know every aspect of injection molding before you pay for it. Then you can decide if the process is suitable for you.
Top 4 pros of injection moulding
1. Fast production, high output rate, and efficiency.
Once new molds are designed and finished, the injection molding machine can produce a large number of products at high speed. And there will be fewer chances of human errors.
2. Product consistency
Since you use the same molds and the injection moulding process is repeatable. Therefore the last product will be the same as the first one. So it ensures consistent parts.
3. Cost-effective for huge production
Injection molding is very suitable for huge-volume orders at a cheap price. Once you start to produce, the cost of a single part is pretty low.
4. Variety of material and color
Once you have the molds made, you can choose whatever material and color you like or need for the parts. And the material you use directly decides the texture of your products. And the texture is also affected by the mold also affects the texture. Therefore you have a wide selection of materials, colors, and textures for custom products.
Other pros of injection moulding
5. Suitable for enhancing product strength
If you want to produce strong and durable parts for some special applications, fillers (e.g. fiberglass) would be a good choice. Though it will reduce the density of the material, great strength will be added to the molded part.
6. Less manual labor involved
The injection moulding process is very highly machine orientated. So an operator can manage almost the whole manufacturing process. In other words, it doesn’t need many workers to operate it.
7. Low waste, environmentally friendly process
Injection molding can produce less waste compared with other traditional manufacturing processes. For the waste can be reground and recycled later. And the waste gas will be collected, purified, and dealt with.
8. Little extra work once products are produced
There is often very little extra work once products are finished. Because parts usually have a finished appearance. For example, when you manufacture keys, they are almost perfect once finished. You don’t have to grind or polish them.
Cons of injection moulding
1. High initial mold cost
Before starting the injection molding process, you need to design and create the molds. But it can take a lot of time and manpower to carry on. That means a high expense. If you have orders of small quantities, injection molding is not suggested. Because every unit of the product is so expensive in this way.
2. Higher requirements for skilled workers
There might be many defects during the injection molding process like flow lines, sink marks, vacuum voids, and so on. To reduce or even prevent these injection molding defects and manufacture high-quality parts, a professional and reliable factory with a group of skilled workers is indispensable.
3. Long initial time
It takes about 15-20 days to design, create and make a new mold. Sometimes it can be months or even longer, all depending on the complexity of your project.
4. Design restrictions
The limit for large parts is around 60 cubic inches. For something bigger, injection molding cannot achieve it. Still, you can choose another manufacturing method like plastic fabrication. What’s more, the mold includes two halves to pull apart easily. So you have to design the mold like that.
5. An accurate cost budget is hard to do
Generally speaking, injection molding fees consist of costs of molds, labor, and material. Because there are uncertainties in the 3 parts, it’s very hard to do an accurate cost budget. Even if a professional group, they can only offer you a relatively accurate cost evaluation.
Factors you consider for injection molding services
As mentioned above, the process seems complex because of many disadvantages and uncertainties. Thus you need to take into consideration some crucial factors when choosing injection molding services.
1. Great design team
Design is one of the most significant factors of injection molding. Choosing a reliable company with a great design team determines the quality of the final products. Because a professional design team will offer you a precise design concept and help you to achieve it. No matter you are a newbie in the industry only have the idea of the product and mold, or you are an expert with many requirements.
2. Quality & efficiency
To offer clients the best service, an experienced injection molding company should have high-quality and efficient machines with skilled workers to operate. What’s more, a good company will be compliant with your products’ specifications and make sure parts pass inspections and meet safety and quality standards.
3. Wide material selection
A good company can offer a wide material selection like plastic(PP, PS), rubber, and metal to meet all your requirements. Since the parts are applied to different industries, and different materials have different characteristics like high flexural strength and elasticity. To learn more, please refer to the chapter below.
4. Time
Time the whole process takes depends on the complexity of your project. However, you can discuss all stages of the time earlier. Because it will help the company have a good way of dealing with clients’ projects and managing the team efficiently. That is important for a professional company.
We StrategicSourcing have long-term cooperation with lots of well-experienced factories. So we offer professional services of changing and creating molds efficiently. And we offer you a wide material selection for custom products like daily products at a competitive price. What’s more, we help ensure product quality and avoid troubles like reproduction.
Comparison of 3 common injection moulding materials
Plastic is the first material type used in injection molding. It can date back to 1872 when Isaiah and John Hyatt invented the first machine and patented it.
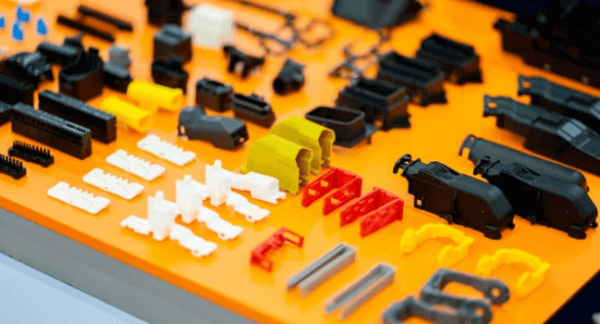
Afterward, many other materials like rubber and metal are used in injection molding. These materials are all common in being melted at a certain melting point, injecting into the mold through a runner, and solidifying into the shape you want after the material cools in the mold.
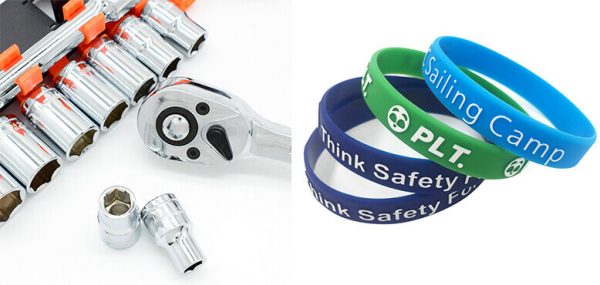
Different materials almost have the same basic process as plastic ones except for some small differences. Since plastic injection molding is the origin, so I compare rubber and metal two materials with plastic below for your better understanding.
Difference between rubber and plastic injection molding materials
- There will be more pressure during the rubber manufacturing process.
- There will be less molding cycle time during the rubber manufacturing process.
- Rubber is cured in the process, while plastic is not.
Besides, a rubber injection molded product differs from a plastic one in the shore hardness. However, the shore hardness of rubber is lower. For example, the shore hardness of a silicone baby plate is 75, while the common plastic parts are nearly 100.
What’s more, according to our common sense, rubber products feel softer, more comfortable, and more elastic compared with plastic ones. So you can distinguish them by touching them.
Difference between metal and plastic injection molding materials
The difference between plastic and metal injection molding is that the former injects a kind of melted polymer into the mold, while the latter injects the metal power and blinder. Here is a picture of the metal injection molding process.
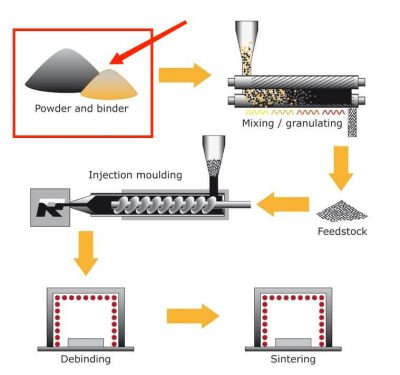
Image Source: AZoM
Common plastic injection moulding materials
When it comes to plastic injection molding, we think about PP and PS. Here also are many types of common plastic material. Let’s have a look.
1. Polypropylene (PP)
Characteristic: thermoplastic, the second most commonly used plastic. Pure PP has the lowest density.
Advantage: readily available, relatively cheap, high flexural strength, slippery surface, high moisture/chemical resistance, stable shape, recyclable four times.
Disadvantage: UV light degradation, extremely flammable, easily dissolves into harmful material above 100° C, difficult to paint.
Application: children’s toys, storage containers, sporting goods, packaging, appliances, and power tool bodies.
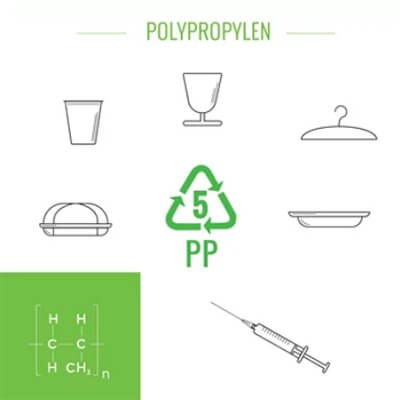
2. Polystyrene (PS)
Two types: general-purpose polystyrene (GPPS), and high impact polystyrene (HIPS).
Characteristic: Both are opaque both predictable and uniform shrinkage. HIPS – brittle, less dimensional stability, a glass-like clarity.
Advantage: inexpensive, lightweight, resistant to moisture and bacteria, excellent resistance to gamma radiation, good chemical resistance to diluted acids and bases.
Disadvantage: flammable, susceptible to UV degradation, poor resistance to hydrocarbon solvents, easy cracking, not biodegradable.
Application: medical, optical, electrical applications(PS) appliances and equipment(HIPS) plastic toys, containers(GPPS)
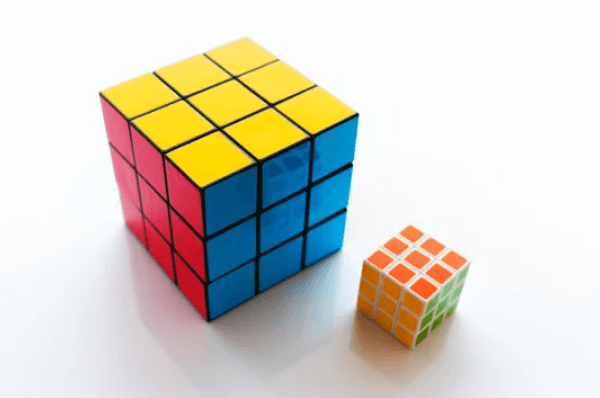
3. Acrylic (PMMA)
Characteristic: a strong, clear thermoplastic, a lighter-weight, a tough alternative to glass, transparent excellent optical clarity.
Advantage: high tensile strength, sunlight/weather/water degradation resistance.
Disadvantage: more costly than glass, prone to scratch, easily stained by greases and oils, low service temperature, low solvent resistance, easily stress cracking.
Application: acrylic boxes, windows, greenhouses, solar panels, boat builders, outdoor signage, and other transparent components for architectural and lighting applications.
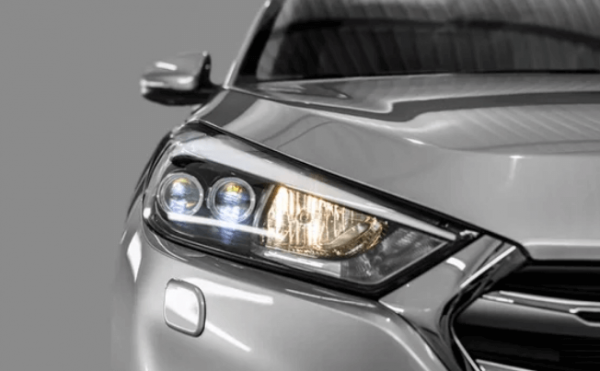
4. Acrylonitrile Butadiene Styrene (ABS)
Characteristic: an engineering-grade thermoplastic, a relatively low melting point, high strength, and impact resistance.
Advantage: being tough and relatively inexpensive, good resistance to heat/oils/acids/alkalis.
Disadvantage: weak resistance to sunlight or weather, dense smoke when burned (The gas has some toxic effect on people, but not too much), poor resistance to high friction.
Application: electronic components, keyboard key, consumer goods, sports equipment, and industrial fitting; automotive components-wheels covers, auto body parts.
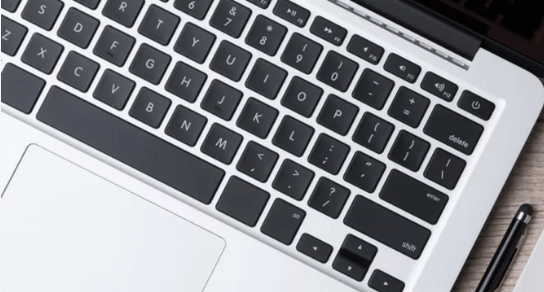
5. Nylon Polyamide (PA)
Characteristic: a large group of materials (natural or synthetic), prone to shrinkage.
Advantage: high heat/abrasion/good fatigue resistance, noise dampening, low coefficient of friction, toughness.
Disadvantage: poor resistance to strong acids/bases/sunlight; no inherent flame resistance (not very suitable for products with high requirements for fire performance).
Application: strong mechanical parts such as bearings, bushings, gears, slides; toothbrushes, wheels, medical implants.
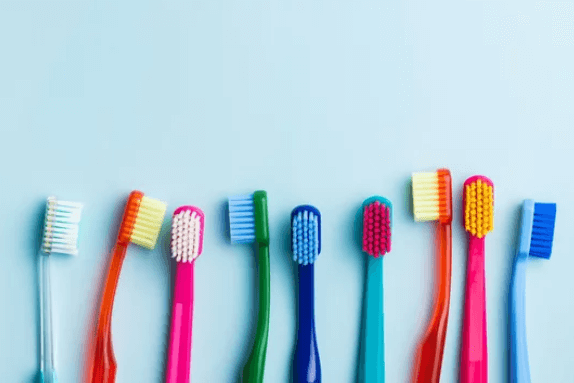
Injection molding applications in daily product industries
Household products
Let’s have a trip to your house. And you’ll find many injection molded products and parts everywhere, such as the toys, the watch, the fruit plates, the cups, the chairs, the trash can, the computer, etc. In a word, almost all electronics are injection molded products and parts.
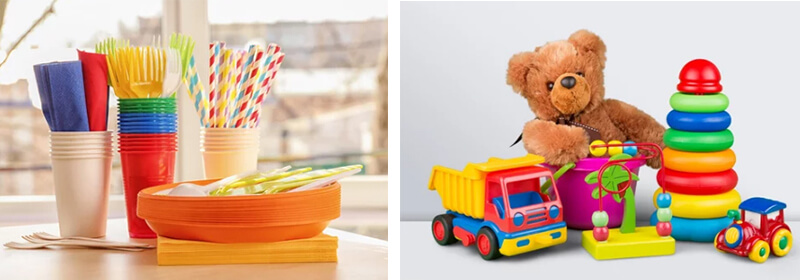
So injection molded products and parts are everywhere in our daily life. It’s a huge market with considerable profit. We always help many clients source and customize injection molding parts in the household industry. If you need help, please CONTACT US at once.
Food and beverage
It’s very important to use safe injection molding products connected with food and beverage. Because these products have a direct relation with our consumers’ health and safety. So injection-molded products should be compliant with industry regulations and certifications like BPA-free construction and FDA certification. And that make sure the process components, food containers, and others are all food-grade.
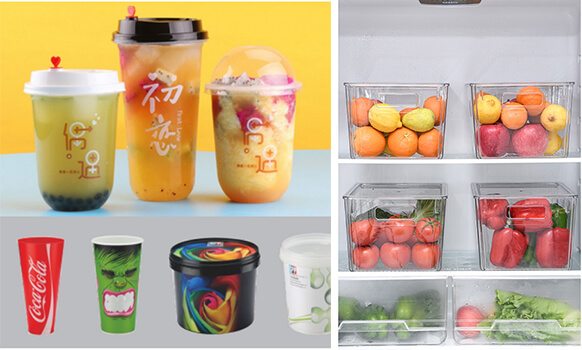
We Jingsuorcing adheres to the standards strictly for all the food and beverage industry products. If you need any injection molding parts in the food and beverage industry, please CONTACT US at once.
Other applications of injection moulding
Building and construction industry
Because of the special characteristics of some materials, injection molding parts have become more important to the construction industry. You can find various injection molding parts in some tools of building, walls, windows, pipes, doors, heavy equipment, and so on.
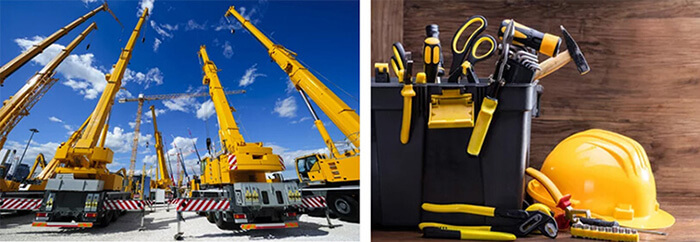
Healthcare industry
Medical products like disposal syringes, test tubes, thermometers, etc. are highly in need against the background of COVID-19. They are all injection molded parts. Here are common medical products below.
- Beakers, test tubes, and other containers
- Housings and casings for medical and laboratory equipment
- Surgical equipment and components
- Drug delivery equipment and components Orthopedics
The material used must be durable, sanitary, and stable. Of course, it’s even stricter than household products. As products have to compliant with more considerations like FDA regulations and ISO certifications.
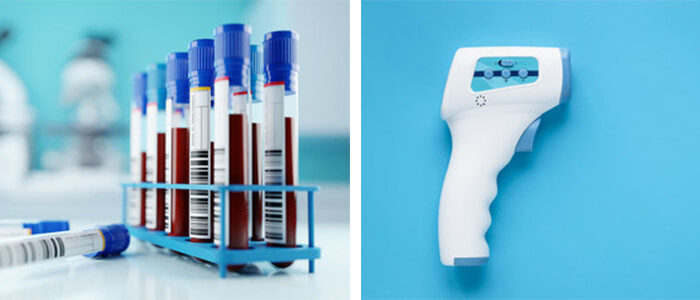
Automotive industry
The injection molding manufacturing process makes it possible to get automotive parts made of all kinds of materials. At first, the material made of cars is almost entirely metal. Gradually, plastic and other material are used in the automotive industry.
Both exterior and interior automotive components can be injection molding parts, such as interior surfaces, grilles, bumpers, door handles, door panels, air vents, dashboards, etc.
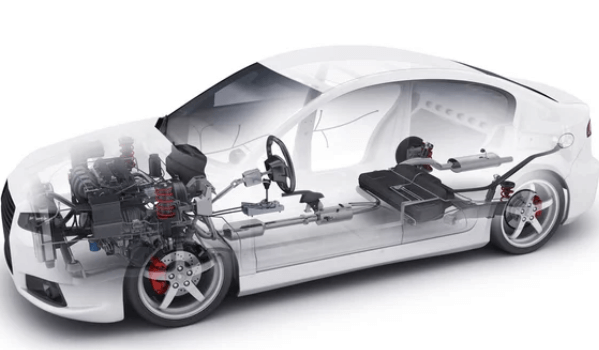
Conclusion
I hope you learn more about injection molding for your custom business. If you have any questions or different ideas, leave your comments below.
As the leading China sourcing company, we StrategicSourcing help you find reliable injection molding factories, get competitive prices, follow up production, ensure quality and deliver products to the door. In a word, our sourcing experts can offer everything you need. Directly CONTACT US, getting guidance step by step.