Before accepting a batch of goods from your supplier, you will do a quality inspection to find whether this batch of goods meets your requirements and decide whether to accept it based on the inspection results.
AQL Sampling is widely used in product inspection because it is more cost-effective than 100% inspection. When your goods are not in a small volume, it is impossible for you to inspect every unit as it will cost you a lot of time and money.
Thus, having a clear understanding of AQL inspection will be good for your business. And this article is complete guidance about it from the following aspects:
What Is AQL in Sampling Inspection?
Sampling inspection is a common method of product quality inspection. A certain number of products are selected randomly from a batch of goods to inspect and find defects. The inspection results will determine whether these goods are “pass” or “fail”.
AQL (Acceptable Quality Limit), once known as the acceptable quality level, is the reference and standard of product sampling inspection. It determines the maximum defective rate you can accept for a batch of goods.
Note that AQL inspection does not guarantee your products are free of defects. It only tells you whether your product defect rate is within your acceptable range through sampling inspection.
Under normal inspection, AQL ranges from 0.065 to 6.5, such as AQL 1.0, 1.5, 2.5, 4.0, etc. The larger the AQL is, the less strict the inspection is. and the more defects you can tolerate. For example, AQL 2.5 means that you can tolerate defects that are no more than 2.5% of the total finished products, and AQL 4.0 means no more than 4.0%.
But in fact, the amount of defective products is not calculated by product quantities * defective rate. They are just specified numbers. For example, you set AQL at 2.5. If you inspect 200 products, there can be up to 10 defective products, rather than 5 (200*2.5%). In the same way, when 500 products are inspected, defects should not be more than 20, not 12.5 (500*2.5%). You can find these numbers on AQL chart. And please read on to know how to read AQL table.
How to Set AQL Levels?
Among these different AQL levels, you need to choose the most suitable AQL for your products and quality requirements.
Different industries have different conventions for the AQL limits. Generally, the metal processing industry will choose AQL 1.0, the electronics industry will choose AQL1.0 and 0.65, and the clothing industry will choose 2.5 and 4.0.
In practice, for most consumer goods, you can set AQL for each type of defects in one inspection like this:
- AQL 0 for critical defects: a defect that may result in a hazardous or unsafe condition for the user, violate regulations, or cause the product unusable, like there are needles or pieces of metal in garments. No such defects can be accepted.
- AQL 2.5 for major defects: a defect that can reduce the usability and sales of products, such as defective function, wrong packaging, product deformation, incorrect size and color, etc. They are the most common product defects and end-users will not accept them.
- AQL 4.0 for minor defects: a small defect in product appearance, packaging, etc, such as fold marks on finished garments. End-users will not mind it or even notice such defects.
Of course, you can set AQL based on your real situation, as it is flexible. For example, you can use AQL 1.5 for major defects, instead of AQL 2.5, which means you have higher quality standards and requirements for your products. In this condition, inspectors need to check more products and inspect more carefully to find more defects, which will also increase your costs.
How to Select Inspection Levels?
AQL level and inspection level together determine how strict quality inspection your product will undergo.When doing AQL inspection, you not only have to set AQL levels, but also select inspection level. They are both based on your tolerance to defects.
Inspection level is determined by GB/T 2828.1. There are general inspection levels (I, II, III) and special inspection levels (S1, S2, S3, S4).
In most condition, you can choose general inspection level Ⅱ. If your requirements for defective products are relatively low, you can choose Level I. If you are quite strict with defects, you can choose Level III.
Compared with general inspection level, special inspection level is less strict. For example, suppose you want to randomly select some cups from 200 cups to check the quality, you need to inspect 32 cups if at general level II, but only 5 cups if at S2.
So when the inspection cost is extremely high, or the product is expensive but will be damaged during inspection, to reduce inspected products, you can choose special inspection levels. It can help you reduce inspection costs and the damage to your products, but is also more likely to misjudge product quality.
How to Use AQL Chart to Make Sampling Plan for Normal Inspection? (Step-by-step Guide with Example)
After setting the inspection level and AQL level for your inspection, you can start making the sampling plan with AQL chart. There are two AQL tables. They work together to determine:
- Sample size: The amount of products to be inspected from a batch of goods
- Acceptance number: The maximum amount of defective products you can accept for a batch of goods
- Rejection number: The amount of defective products to reject a batch of goods
Now assuming that you have 400 pieces of dresses and you select General Inspection Level II, AQL 2.5 as the inspection standard, let’s see how to use the AQL sampling table.
Step1: Choose Lot Size According to Your Product Quantities.
Lot size is on the AQL chart 1. It is shown as a range of product quantity, such as 2-8, 9-15, 16-25, etc. If you have 400 dresses, the lot size is 400 and you should choose the range: 281-500.
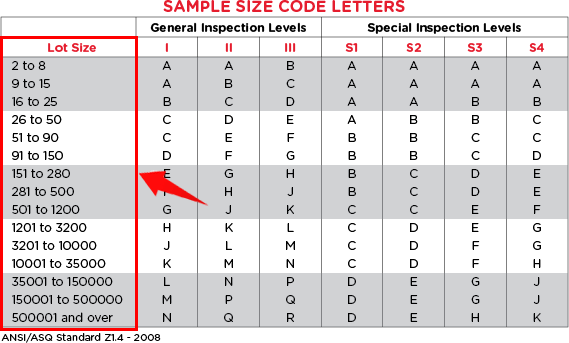
Step2: Obtain Letter Code According to Lot Size and Inspection Level You Set.
Then, at the intersection of lot size (281-500) and level II, you can get the letter code H, as the picture shows. It will be used to find sample size, acceptance number and rejection number on AQL chart 2.
Step3: Obtain the Sample size, Acceptance Number and Rejection Number
Now let’s move to AQL chart 2. Next to the letter code H, you can get the sample size 50, which means 50 pieces of your total 400 dresses should be inspected.
At the intersection of letter code H and AQL 2.5, you can find the acceptance number is 3 and the rejection number is 4. i.e. Among these 50 units, if 3 or less defects are found, you can accept this batch of goods. If 4 or more defects are found, you can reject this batch.
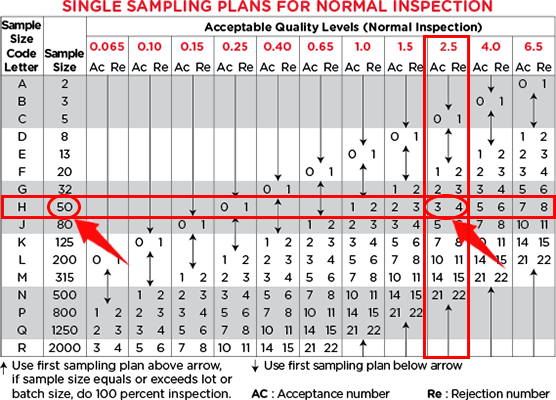
So in this example, the sampling plan should be:
- Lot size: 400
- Inspected at level II,
- AQL2.5
- Sample size: 50
- Acceptance number: 3 ( 3 or fewer defects found, pass)
- Rejection number: 4 (4 or more defects found, fail)
Special Situations You Are Likely to Encounter When Using AQL Chart.
Generally, you can get a sampling plan through the above 3 steps. However, in some situations, it will be a little different.
When You Find Up Or Down Arrow at AQL Chart
If your product lot size is 20 and will be inspected at Level II, AQL 1.0. According to steps 1-2, you will know the letter code is C. But at the intersection of Letter C and AQL 1.0, you can only see a down arrow, rather than specific acceptance or rejection numbers. In this situation, you should use the plans below the arrow, as the following picture shows.

Thus, the sampling plan should be:
- Lot size: 20
- Inspected at level II, AQL1.0
- Sample size: 13 (not 5)
- Acceptance number: 0 ( no defects, pass)
- Rejection number: 1 (1 or more defects found, fail)
When the Sample Size Equals Or Exceeds Lot Size
Now if you inspect 20 products at Level II, AQL 0.25, there will be some other differences. At the intersection of Letter C and AQL 0.25, you will see a down arrow again. You must have known that you should use the plan below the arrow. But you will find the sample size is 50, which is larger than your lot size (20).
In this situation, when the sample size equals or exceeds lot size, you should conduct a full inspection. That means each product should be inspected.
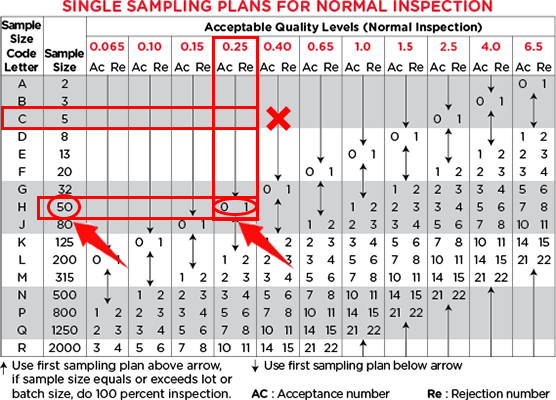
In this case, the inspection plan should be:
- Lot size: 20
- Inspected at level II, AQL 0.25
- Full inspection (not sampling inspection)
- Acceptance number: 0 ( no defects, pass)
- Rejection number: 1 (1 or more defects found, fail)
AQL Calculator
From the above steps, you can feel that there is actually no AQL formula and no need to do calculations. All you have to do is find some numbers step by step in AQL charts. Some inspection companies offer AQL calculator service. You just need to fill in lot size, inspection level, and AQL level as the following picture shows, then you will get the sampling plan. It is much more convenient and quicker.
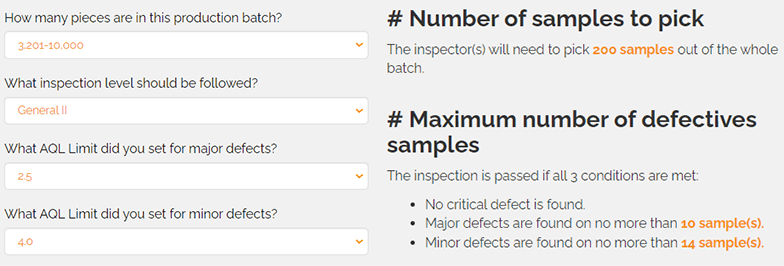
The End
Hope this article can help you use AQL in sampling inspection correctly. If you have any questions after reading this simple guide, leave a comment below.
We are StrategicSourcing, a leading Chinese sourcing company. We have supported the businesses of 4000+ clients, by offering them good services and solutions to any problems, including buying, customization, product inspection, shipping from China, etc. If you need help, please feel free to CONTACT US.